The ME 72 Competition
This amphibious robot competition is the culmination of two academic terms of work by small teams of mechanical engineering juniors and seniors. The ME 72 capstone course has existed for 35 years as an annual competition. The "game" is invented each year by the incredibly dedicated Professor Mello and his team of teaching assistants, most ME 72 veterans. The name of the competition, once the rules are unveiled in the fall, is chosen by the course's students. My meme-y suggestion for the challenge set in Caltech Pond* ... a suggestion I never expected to win... won. And ironically I haven't, uh, actually even seen Star Wars Episode III. Sue me.**
Competition day is a big production complete with audience and announcer, but what the audience sees is a tiny fraction of the process and an even tinier fraction of our grades. The real emphasis is on learning and collaborating, making progress, gaining familiarity with the design cycle, going through design reviews, and really *really* internalizing the lesson that it can't just look good in CAD... it also has to work in real life. It was overall a very positive environment in which to learn, with by-and-large a far greater spirit of helpfulness and camaraderie than unhealthy competition between teams. Because really, we were all there together, in the machine shop at 1 AM, to build cool robots with our classmates.
* NOTE: the pond was called "Millikan Pond" at the time of the competition, as it was named after the scientist... and prominent eugenicist. I was excited to support the ultimately successful movement to rename the pond and building and remove Millikan's name. Therefore, I've changed all references to the library and pond on my website to reflect the shiny new eugenics-free name. However I did want to note that the original competition name was "It's over Millikan, I have the high ground!" since "Millikan" sounds a lot like "Anakin" and the joke makes more sense.
** Please don't sue me.
Game Basics
"Teams must design, build, and operate three amphibious, remote-controlled robotic vehicles to play a game best described as 'control point domination.' Teams will compete [one-on-one, i.e. three bots vs. three bots] to accrue the most points during five minutes by temporarily 'controlling' various scoring elements by depositing or shooting a ball into them. Robots must successfully navigate both land and water environments, obtain balls from dispensers, and shoot or deposit them into goals to score. The tournament will consist of a round-robin and single-elimination rounds. The competition arena is within the 42 x 51 ft rectangular section of [Caltech Pond] between the east wall of [Caltech Hall] and the arched pedestrian bridge."
--- Game Manual: Introduction
Hence, "I Have the High Ground"
Goals! The various types are pictured below:

Dispensers release a ball when a button is pushed.
3-Level Goals
Center Island, featuring four static ramps and a rotating middle with a scoring bucket in the center
Bots begin the match at the one of the two ramps
Dimensions in inches of each 3-level scoring tower goal. Images taken from game manual. Levels will be referred to as "low", "middle", and "high"
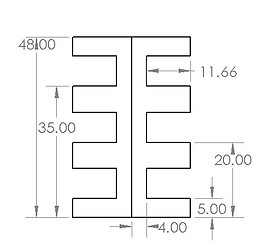

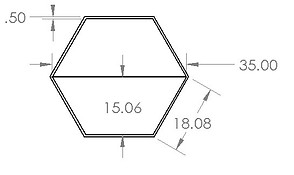
Team Creatures of the Deep
Our team of five juniors decided on the team name "Creatures of the Deep" so that we could name our robots after sea monsters --- Jörmungandr, Nessie, and Cthulhu! ME 72 was a real learning experience for us (translation: we navigated quite the slew of setbacks and added a lot to our design intuition and understanding along the way) but I'm glad it was a learning experience. It made me a much better engineer and gave me a chance to take a real stab at leadership in design work.
As a team we had a tendency to take unconventional routes in design rather than sticking with tried-and-true methods of ball shooting and amphibious locomotion. I wouldn't call it re-inventing the wheel, though... more like inventing an exciting new alternative to the wheel with great potential. This ambitious insistence on creativity may have dragged us more than a bit behind schedule, but taking the course as an opportunity for skill-building, not for a trophy, I'm glad that it's the route we took.

A button I made with our team name, "Creatures of the Deep"
I also learned a lot about working on a team. Selecting a "team leader" early on was an excellent suggestion by one of my teammates. The team member who stepped up to the role did a great job, reaching out to team members on their progress and making sure that nothing administrative --- our finances, weekly reports, etc. --- fell through the cracks. And she was completely humble about the role, serving to hold our team together rather than elevating herself. One thing I would have change, however, is our method of collaboration in design. We divided design tasks individually, leading to a situation where each team member took charge of a subsystem with only rather perfunctory input from others. I am susceptible to believing others know more than I do just because they project more confidence, and didn't realize that in a team of not-so-seasoned engineers, each of us would have benefiting greatly from additional perspectives to catch our mistakes rather than each others' blind trust. As the course progressed, I witnessed the successes and flops of each of our ideas and efforts and got a much better sense of each of our actual skills instead of their flashy or lackluster advertisement earlier on. Although I fully acknowledge the benefits of time to work solo on a project (I for one absolutely need it), I wish we had realized earlier on how much we could have learned from each other when we each had so much to learn.
Meet the Bots

Robot Base and Flotation
The deck of each robot consisted of three layers. In the middle, a low density vinyl foam provided a buoyant material to serve as the base. On either side, a layer of cross-stitched fiberglass was adhered with an epoxy resin to create a strong composite material providing structural rigidity to the deck. Ultimately, this system yielded a resilient yet light-weight foundation for the rest of the robot, and for additional buoyancy, closed-cell foam was strategically velcro-ed below the robot base.
The system worked well in holding our bots together and keeping them afloat, but I can't take much of the credit; this whole deck/flotation design was thought up by one of my teammates!

Propulsion Systems
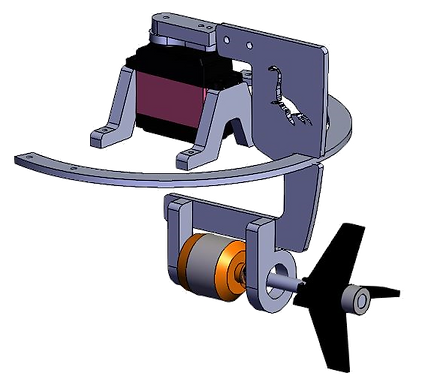
Aquatic Propulsion
Aimed Propeller System
Each of the three robots used an aimed propeller system to cruise Caltech pond. The aluminum propeller spun by a brushless motor and was aimed with a 180 or 270 degree high-torque servo, enabling fast speeds and a tight turning radius. The semi-circular guide rail critically prevented excessive vibration of the system to enable its smooth operation.
I was the driving force behind this design, with help from my teammates on the details, and I'm quite pleased with how it turned out, though it took numerous iterations to get there. Although it could not drive the robot backwards, the aiming system makes tight turns, as demonstrated in the video below.
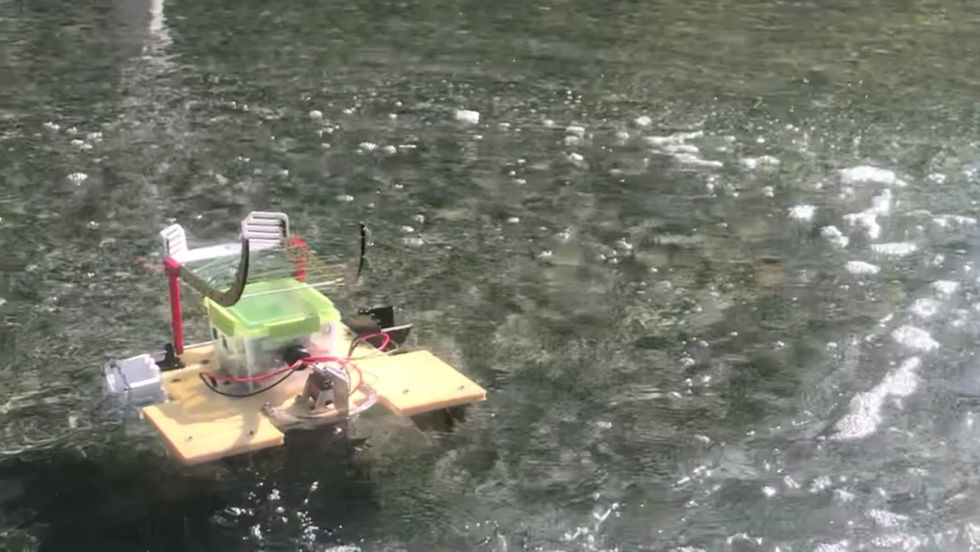
Land (and Water) Propulsion
Paddle Wheels + Custom Transmission
Present only on Jörmungandr, the paddle wheel system allowed the robot to drive up out of the water and navigate the center island. The paddle wheel nature also enabled tight turns and backwards motion in the water if needed (but was much less efficient than the propeller system).
The rules of the course disallowed geared motors for propulsion systems, encouraging teams to design their own transmissions. Originally built with a 9:1 gear ratio transferring rotation from brushed motors to large paddle wheels, torque limitations of the motor necessitated a redesign. The paddle wheels were decreased in diameter to impart more force when driving up the ramp, and an additional stage of gears was added to increase the gear ratio to 16:1.
The video below shows Jörmungandr driving up the center island ramp.

CAD for the 9:1 gear ratio set-up. The 16:1 ratio was created by putting another gear on the wheel shaft and creating a new shaft and mount for the wheel.

Air-Based Propulsion
EDF System
We had originally planned for two of our robots to use an EDF system which would push air to create thrust. Due to unusual shipping issues (translation: ordering parts from China as COVID-19 was beginning to spread was not a great plan... they never showed up), this design did not make it to competition. It worked excellently (but ear-splittingly) when we tested it with three fans that did arrive, but a small design flaw caused some fans to break, and we never received replacements.
I can't take credit for this system, designed by one of my teammates, but it's so disappointing we didn't get to use it that I wanted to give her a shout-out for all the effort she put into it. Moral of the story: choosing reliable vendors is critical.
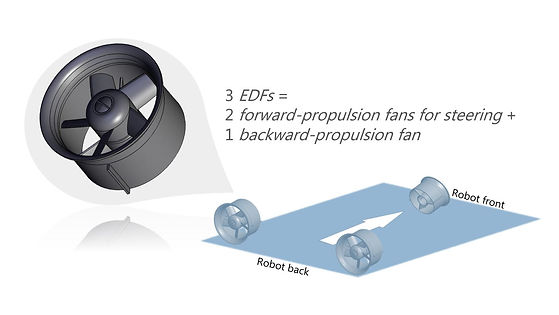
Game Object Scoring and Handling
Our team designed three different systems to handle the game balls and score them in both the center island bucket and the low and medium goals. Our plans to reach the high goal were not able to be built due to time constraints.
Our original task delegation scheme gave the challenge of ball handling to a single teammate building a scissor lift, and putting such a big task on a single person was in hindsight a mistake; the work couldn't get done fast or well enough with one person. Our team leader eventually stepped in and quickly designed and built a very simple basket system for low goal scoring for our scoring and handling demo. Following that demo, I was convinced that being able to scoop from the water would be a major improvement, and devised two different mechanisms: the gated basket, and the arm with flexible scoop. I designed and CADed these designs, and we worked as a team to construct (and in some cases tweak) them.
In hindsight, scooping balls from the water was strategically ridiculous given how tight were were on time: although balls could theoretically end up in the water, the ball dispensers were designed to drop balls directly into a robot. But I dare say there are some pleasingly clever ideas hidden in the mess!

Scissor Lift
Middle Goal Scorer
A
A mistake on so many levels.
Gated Basket
Center Island and Low Goal Scorer + Scooper
My teammate designed a simple, lightweight basket design that could catch balls dispensed from the ball dispensers, ferry them to the center island bucket or low goal, and dump them in. I thought it would be cool if we could also scoop balls from the water, and excitedly designed a passive mechanism basket "upgrade." Looking back, this was the strategically wrong choice: it made the basket much heavier and less capable of holding multiple balls, and its construction took away valuable time and resources. The KISS principle exists for a reason. However, it is entertaining in a reminds-me-of-a-pinball-machine kind of way.

The basket system before and after.
The after video shows the ball being "scooped" (theoretically from floating in the water), rolling into the basket, and rolling out into (what would in action be) the center island bucket or the low goal.

Arm with Flexible Scoop
Middle Goal Scorer + Scooper

STEP 1:
Scoop ball from water
With the flexible scoop in the (a) configuration, the arm reaches into the
water and picks up a floating ball.
The ball drops into the inner chamber. This allows the flexible scoop to invert when gravity compels it to do so, changing from (a) to (b).
The ball rolls back into the flexible scoop, now in the (b) configuration.
I've been told jokingly that this was such a classic mechanical engineer move: think up a passive mechanism in order to avoid adding more electronics. I'm guilty as charged --- I wanted to be able to scoop balls from the water but didn't want to deal with mounting, wiring, and programming a motor or servo on the end of some arm. So I brainstormed this innovative passive mechanism instead. I'm proud of the concept, but fully aware its implementation deserves a redesign given more time.
The diagrams below depict how it works. Please also refer to the light blue box depicting the flexible basket "scoop" and "scorer" positions.


(a) scoop
(b) scorer
The weighted, flexible basket curves whichever way gravity directs it, a key passive mechanism. The two configurations depicted above --- (a) scoop and (b) scorer
--- allow one arm to perform two functions.

STEP 2:
Score ball in middle goal
The flap in front of the inner chamber closes so the ball cannot roll back inside when the arm lifts to score!
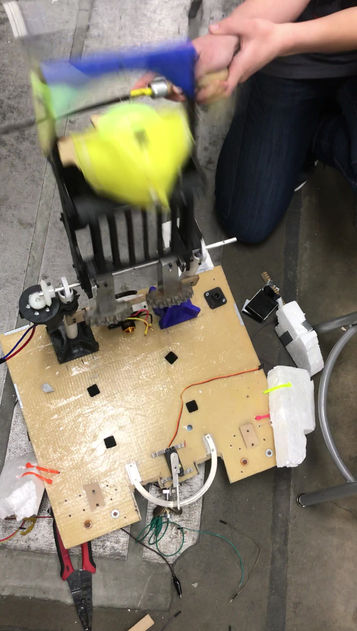
Score! Into the middle level goal!
The accompanying video shows the arm in action, and it's remarkably satisfying; in the water, its middle goal scoring action is reminiscent of a slam-dunk. You will notice, however, a few changes to the CAD: the arm is shorter (necessitating an extra polycarbonate scoop), the inner chamber lighter (thanks to one of my teammates), and there are counterweights. Yes, I originally designed the arm without counterweights. Yes, it definitely needed the counterweights.
I introduced this mechanism as "an innovative passive mechanism whose implementation would have benefited from a redesign if we'd had more time" --- this redesign would consider, at minimum:
-
More elegant counterweights.
-
A much-improved distribution of weight (essential for a craft on the water)
-
A sturdier flexible scoop than the very thin plastic film used.
ME 72 is very fast-paced course, with high expectations in a short time frame. I enjoyed the urgency, but as always yearn for more time: this mechanism is a great first functional prototype, but with more time I could produce a real, quality design.