Instruments R&D Engineering Internship at Auris Health, J&J
My 2019 summer internship at Auris Health, a recent Johnson & Johnson acquisition, was an amazing experience in R&D in the medical robotics industry. I gained insight and experience in so many steps of the design process, from designing and CADing original parts to writing documentation to Instron testing to tolerancing complicated systems in anticipation of ordering custom injection molds. And the friendly, motivated, and collaborative company culture played a huge role in my positive experience. What follows are some shareable projects I was personally responsible for that summer.
Percutaneous Needle-Cannula Connector
Two easy-to manufacture designs
A percutaneous needle has two parts: the needle itself, and a cannula around the needle. The full assembly is inserted through the patient's skin, and then the needle is pulled out to leave only the cannula. Unfortunately, it was easy for these two parts of our vendor's needles to disconnect prematurely. The Instruments group director was in contact with them requesting they alter their design, but in the case that they refused, I was tasked with devising an alternate solution that did not require changes on the vendor's end.
I developed two separate potential designs in parallel, reaching a working prototype for each. Both can be operated with only one hand so the other hand is free to hold the needle/cannula shaft steady, and both are relatively simple to manufacture. For the stretch-over band I tested a variety of rubber sheets from McMaster-Carr cut into the proper shape, and for the snap-together cover I took advantage of Auris's SLA 3D-printers which could handle the small snap-fit hooks.


Instron Test Fixture for a Torsion Spring

Another design project I undertook was a test fixture to measure the force imparted by the ends of a torsion spring. This measurement was important to the spring's application in the subsystem my mentor was designing, and I made sure the test fixture would mimic the spring's real use.
​
I designed the 3D printed fixture, wrote the test script for the Instron, and used it to collect data such as that shown in the graph.

Additional Projects
Instron: Dry + Wet Kinetic Friction Data
More data collection with the Instron: measuring kinetic friction of various materials, when dry and when wet. We hoped to be able to select one of the five materials suggested by a vendor for injection molding the part, and three of the five materials performed well above the minimum friction thresholds required!
Although my mentor had previously designed and 3D-printed most of the test fixture, several issues arose that required my own design additions. The test apparatus closely mimicked the geometry of the actual subsystem, and I continued this careful imitation with my modifications.


Fluid Ingress Testing
This was the project I personally refer to as the "fluid ingress testing saga." Tasked with determining time until leakage for different flow rates, I returned with unfortunate news, calling into question both the system design and the rigidity of the test protocol. What seems a simple task was not: water is messy, results were often inconsistent despite the greatest efforts for consistency, and ensuring that everything was dry between tests was challenging. Difficult but important, I gained experience working on a time-sensitive team setback and collaborating in team meetings.
Tolerance Analysis
This consisted of reviewing a team member's tolerance stacks (making useful comments and catching mistakes) before a critical mold release for a new subsystem's injection molded components. Pictured is a sample diagram I drew for myself to remember the conventions.
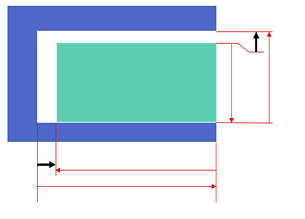
Some Internship Takeaways
Mechanical Engineering Skills
-
Instron/Universal testing machine experience: designing fixtures, writing test scripts (via a GUI), interpreting data
-
Fluidics testing
-
Introduction to the usefulness of master modeling and other Solidworks techniques
-
Design skills
-
Advanced 3D printing materials
-
Tolerance analysis
-
Attention to usability and poka-yoke in product assembly
​Industry Skills
-
Organization and documentation of equipment
-
Communication in the workplace
-
Purchasing prototyping materials, ordering custom parts from companies like Protolabs
-
Writing documentation
-
Understanding the high degree of testing, protocol, and documentation that goes into a product (especially in an industry like medical robotics)